Bulk Type | vs | Thin Film Type |
cm or mm | Unit size | nm (<1/10000) |
15 steps | Process step | 4 steps |
~ 1 month | Process time(1set) | ~ 6 hours |
⬆ | Production cost | ⬇ |
O (Toluene, Benzene) |
Toxic materials | X |
Core Technologies
deposition process
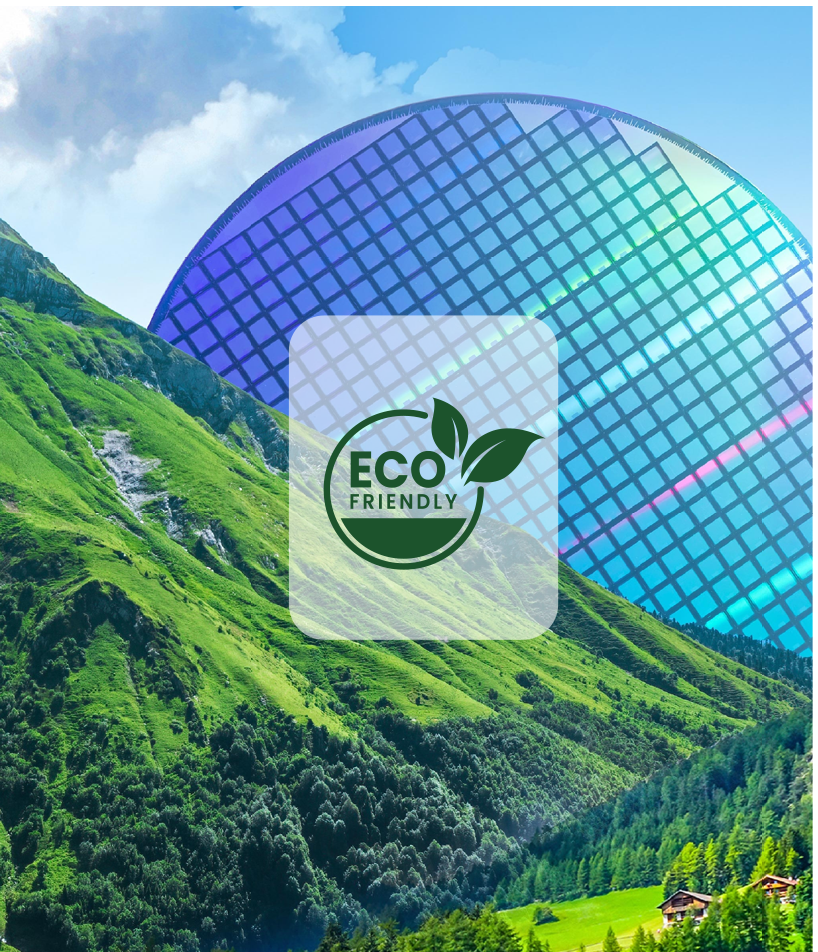
components
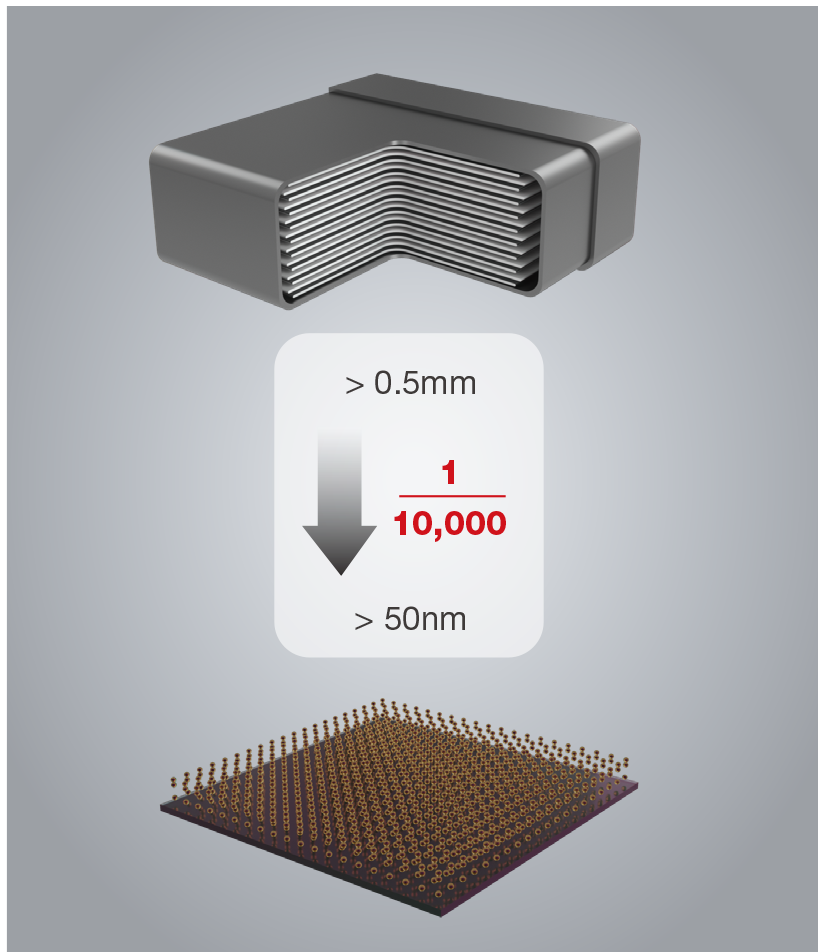
bulk to one chip
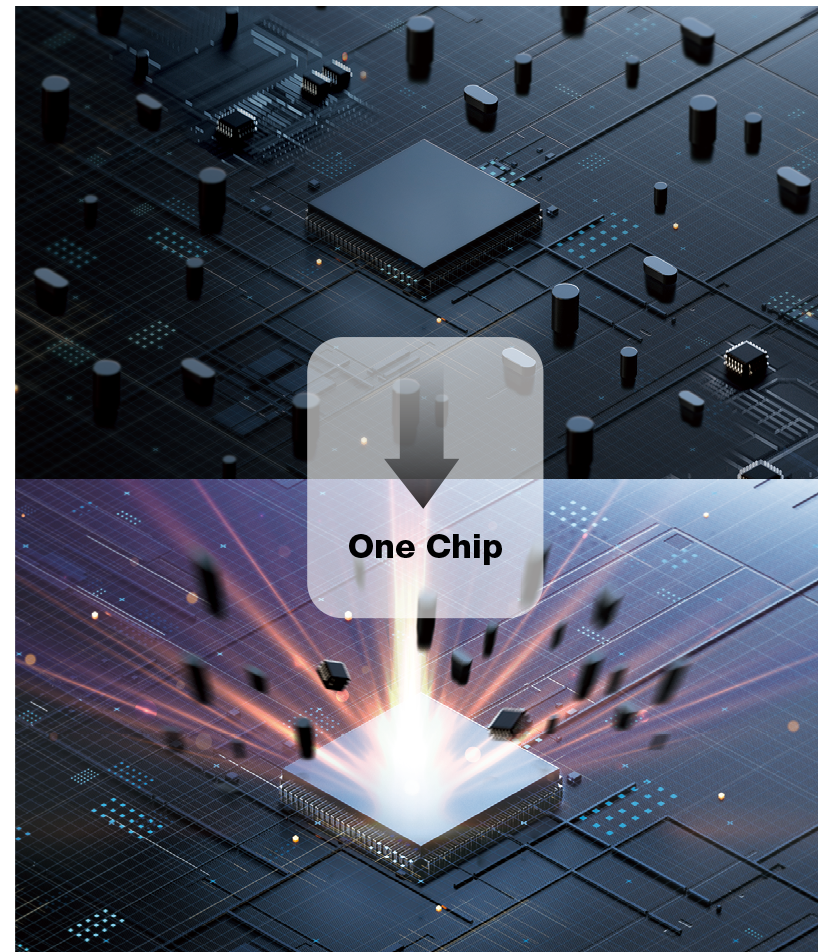
World 1st Multifunctional Energy Responsive Thin Film
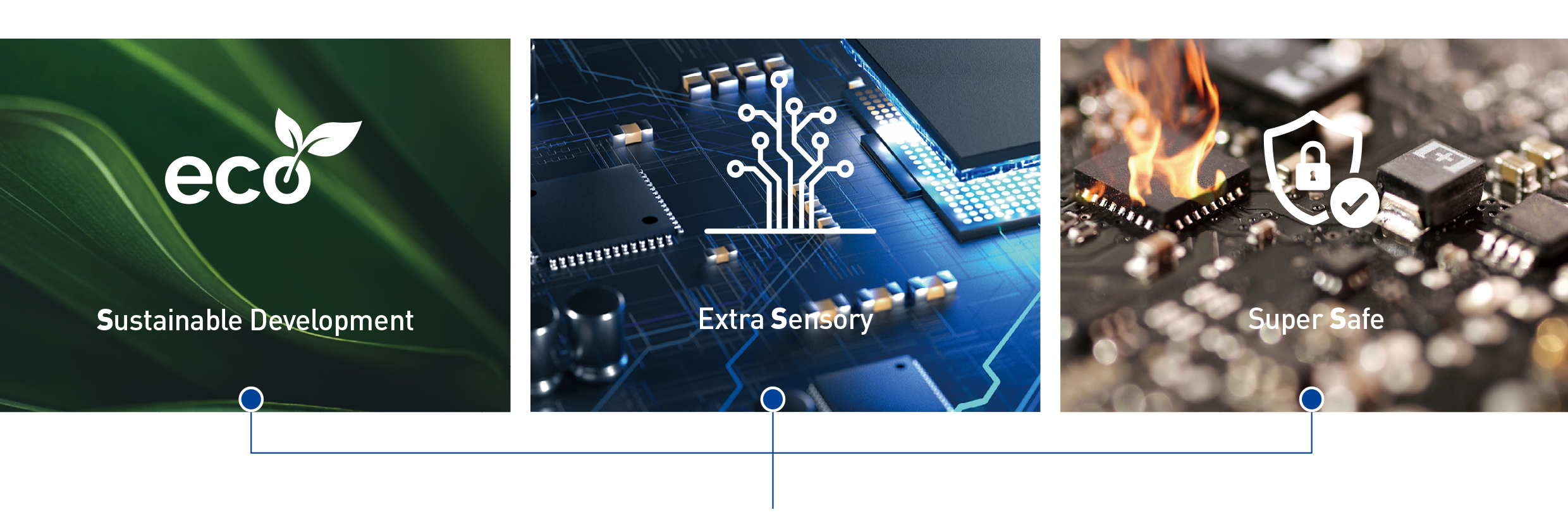
Sensing + Switching function to Thermal or Electrical energy
Fabrication Process
Competitive Price
Function & Performance
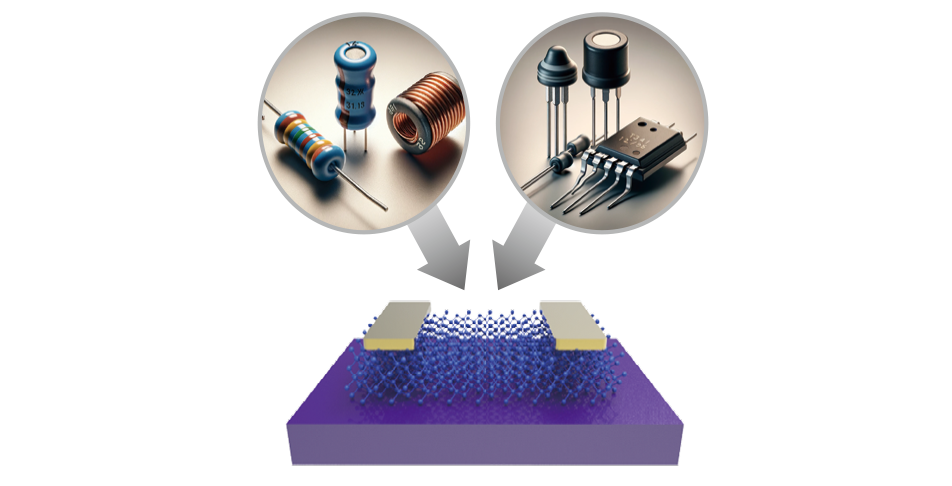
Increased accuracy through system simplification
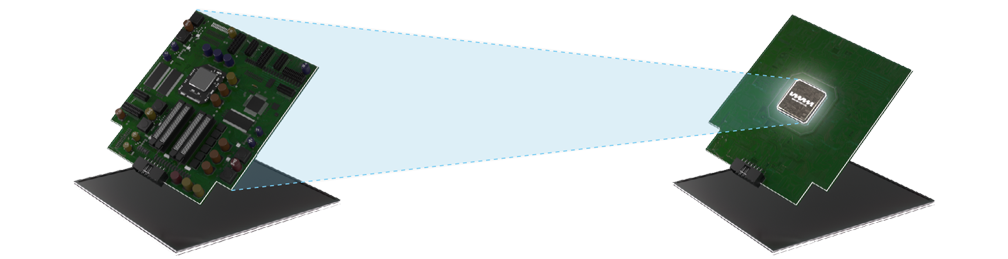
Conventional System
Ultra Simplified System
“Next Generation Thin Film on Emerging Technology”
High-crystalline thin film deposition source technology
PoC in progress with R&D partners
Quantum Computing
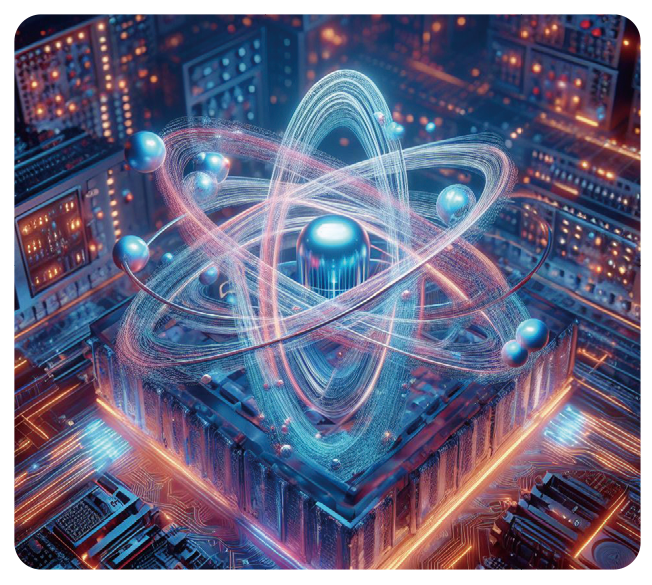
A.I. Semiconductors
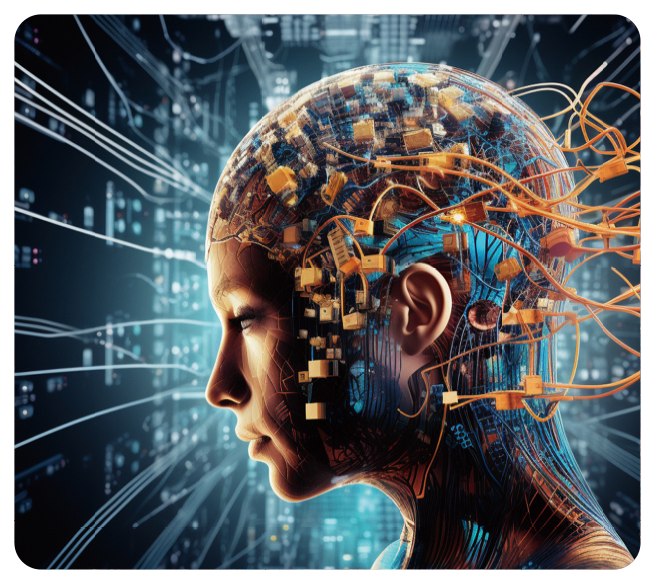
Power Electronics
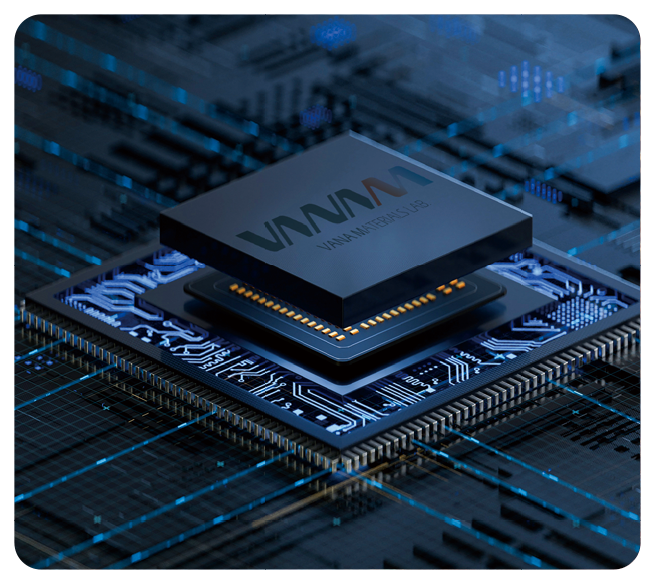
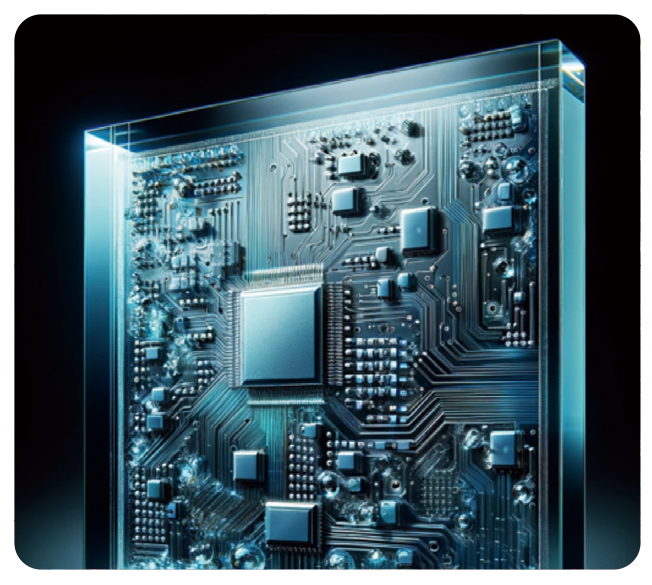
Glass Substrate
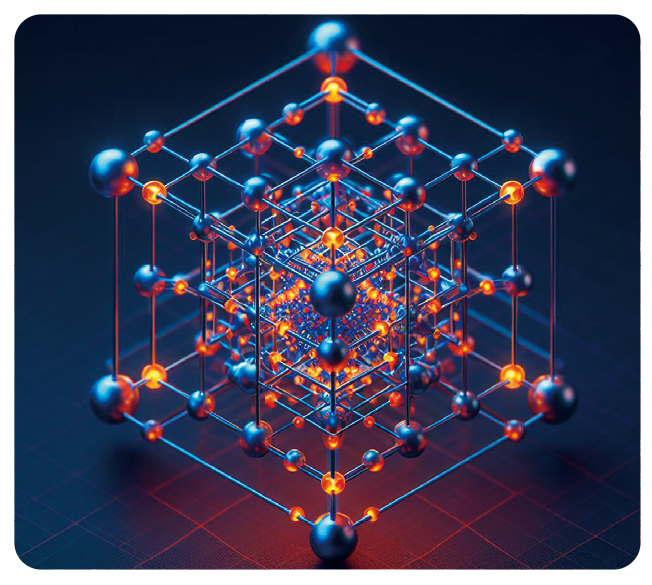
Advanced Materials
Customized Thin Film Deposition Service
to customer needs.
Development of special thin films & deposition process conditions
unavailable in conventional fabs.
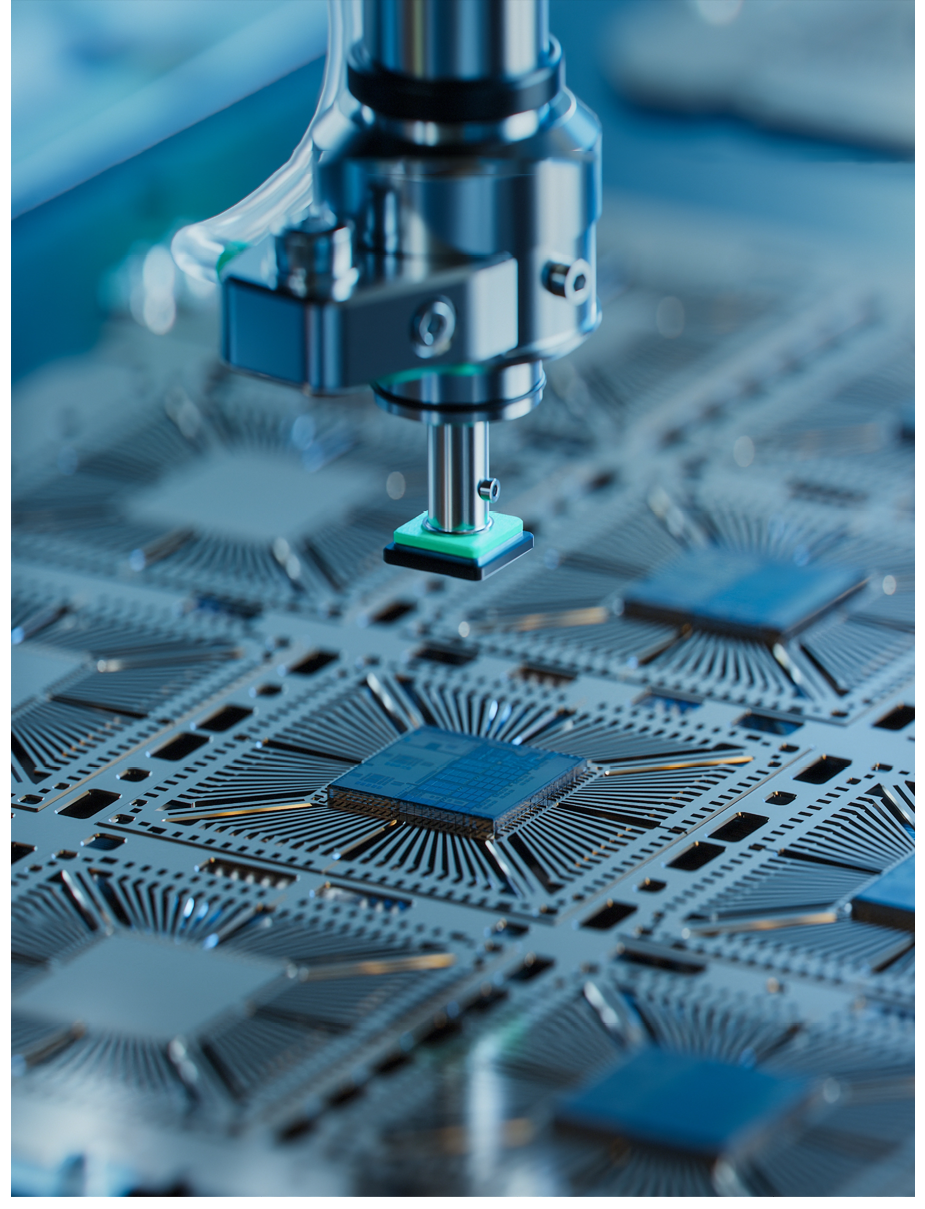
PVD–Sputter & Evaporator
Oxide VO2, V2O5, TiO2, Ta2O5, HfO2, ZnO, ITO, IGZO, …
Nitride TiN, AlN, AlScN, SiNx, …
Metal Au, Pt, Ag, Al, Ti, Cr, Ni, Bi, Mo, Hf, Sc, W
ALD
Oxide Al2O3, HfO2, ZrO2, HZO, ZnO, TiO2, In2O3,
Ga2O3, SnO2, SnO, …
Metal Pt, Ru
Deposition Process

Innovative R&D Service for Thin Film
A.I. development of prediction model
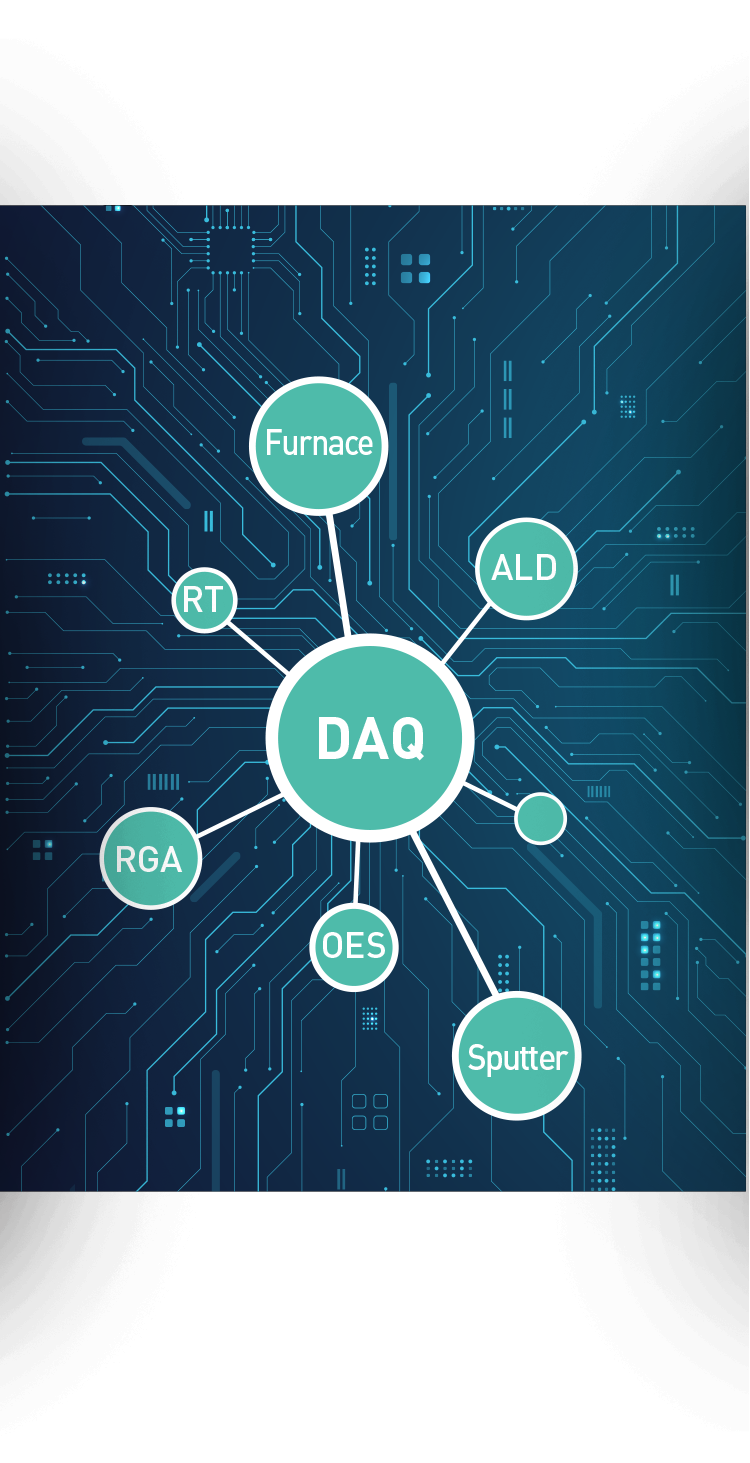
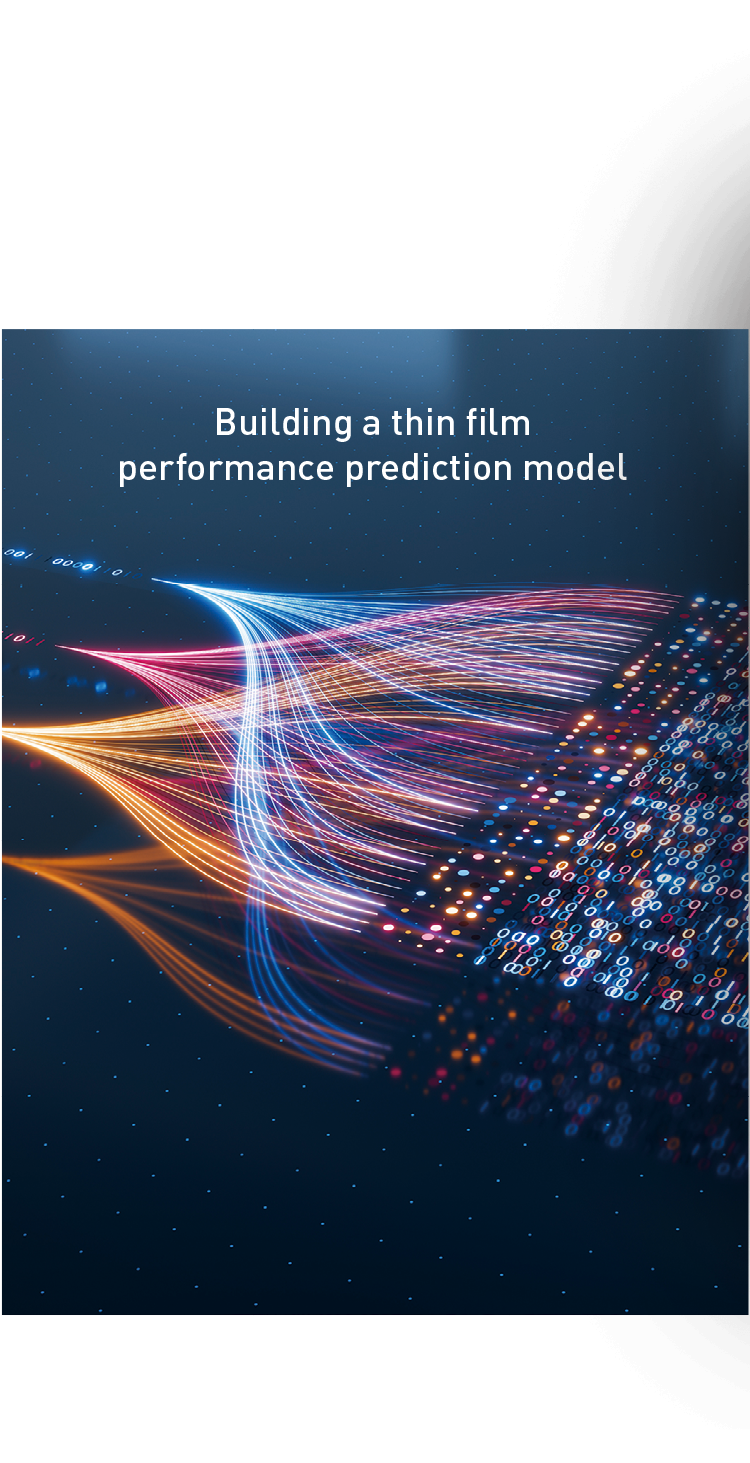
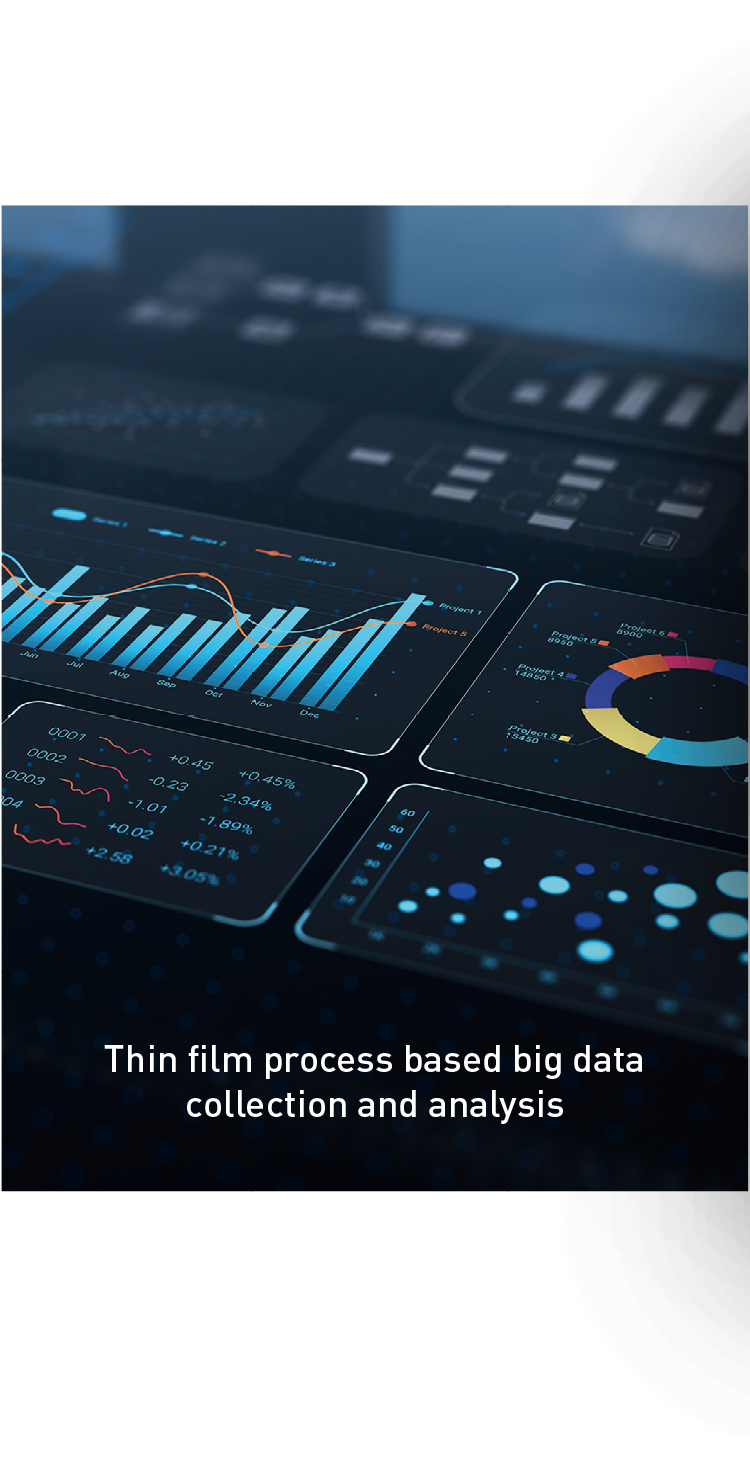
customer request. It also collects and analyzes
data generated during the process to predict
the thin film’s characteristics, dramatically
reducing time and cost
• Desired thin film properties + optimized process
• Device design and Fab-linked device manufacturing service
customer-specific thin film & device analyses,
from non-destructive spectroscopy
to electrical analysis
SEM, TEM, XRD, XPS, UPS, AFM, Raman
• Device characteristic analysis
I-V, C-V, Pulse measurement, Ferro., Piezo.
new material thin film development
• Chemical energy potential calculations for thermodynamics and area selectivity
• Physical variables such as crystal orientation, morphology, and strain
Research Team
• Thin film materials and process technology analysis
• Thin film simulation
• Commercial viability test

Patent Team
• Core IP analysis based on technology verification
• IP portfolio construction
• Technology transfer mediation
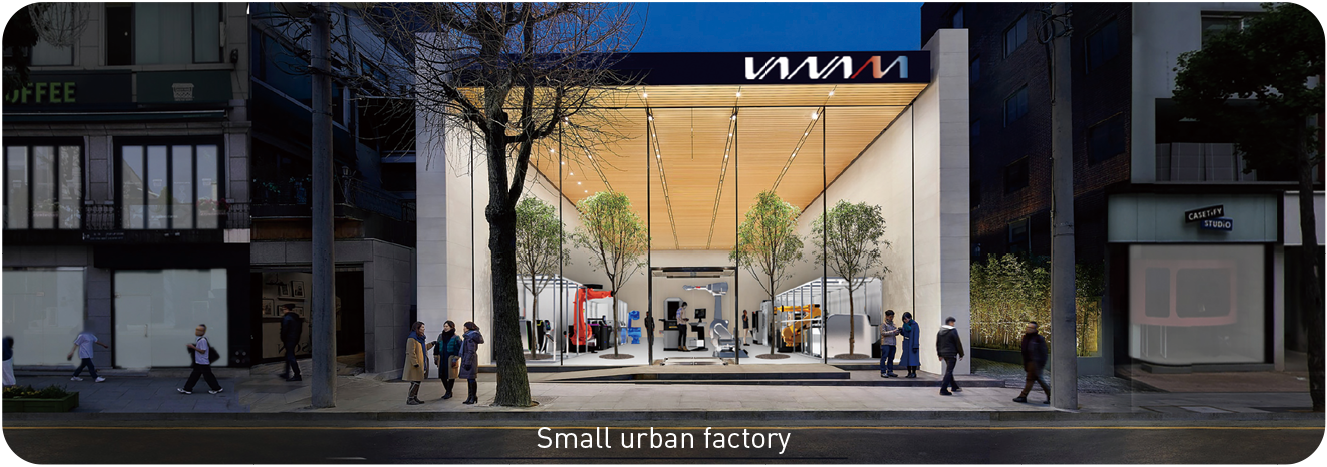
with a team of vacuum equipment
manufacturing experts with over
30 years of experience
VanaM provides process technology and deposition solutions that go beyond simple manufacturing, thereby minimizing the cost and time incurred in the early R&D stages. We have developed special deposition instruments equipped with an additional system that can secure process data such as plasma wavelength and residual gas, enabling thin film performance prediction and process optimization through machine learning.
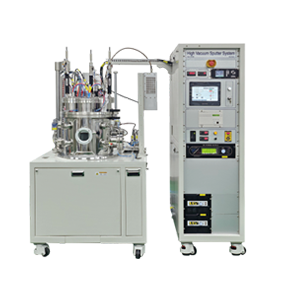
Sputter
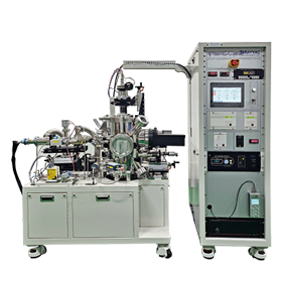
PLD
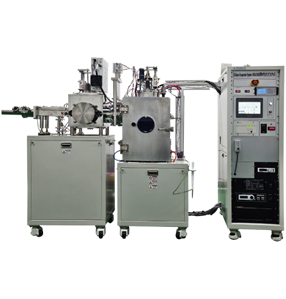
Evaporator
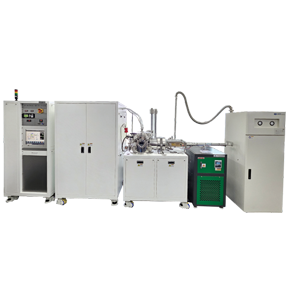
ALD & MOCVD
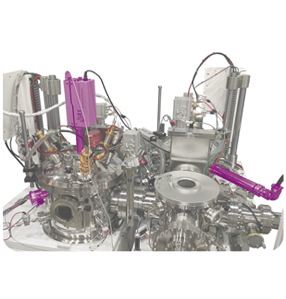
Process Big Data Collection System
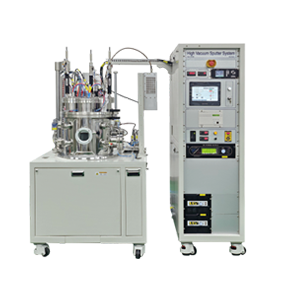
Sputter
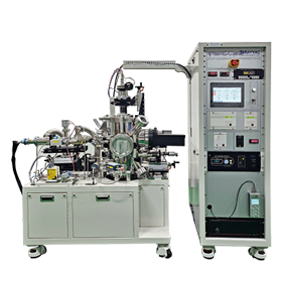
PLD
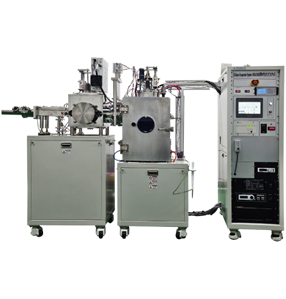
Evaporator
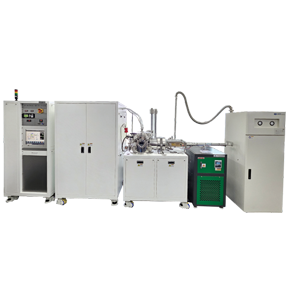
ALD & MOCVD
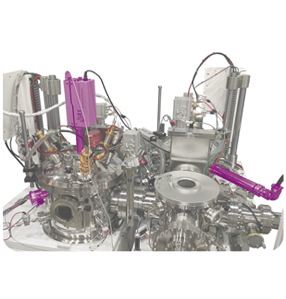